Life size bronze statues are sculptures made from bronze, typically crafted and cast to the proportions of real people or animals. Due to the strength and durability of bronze, these statues can be preserved for long periods and possess significant artistic and historical value.
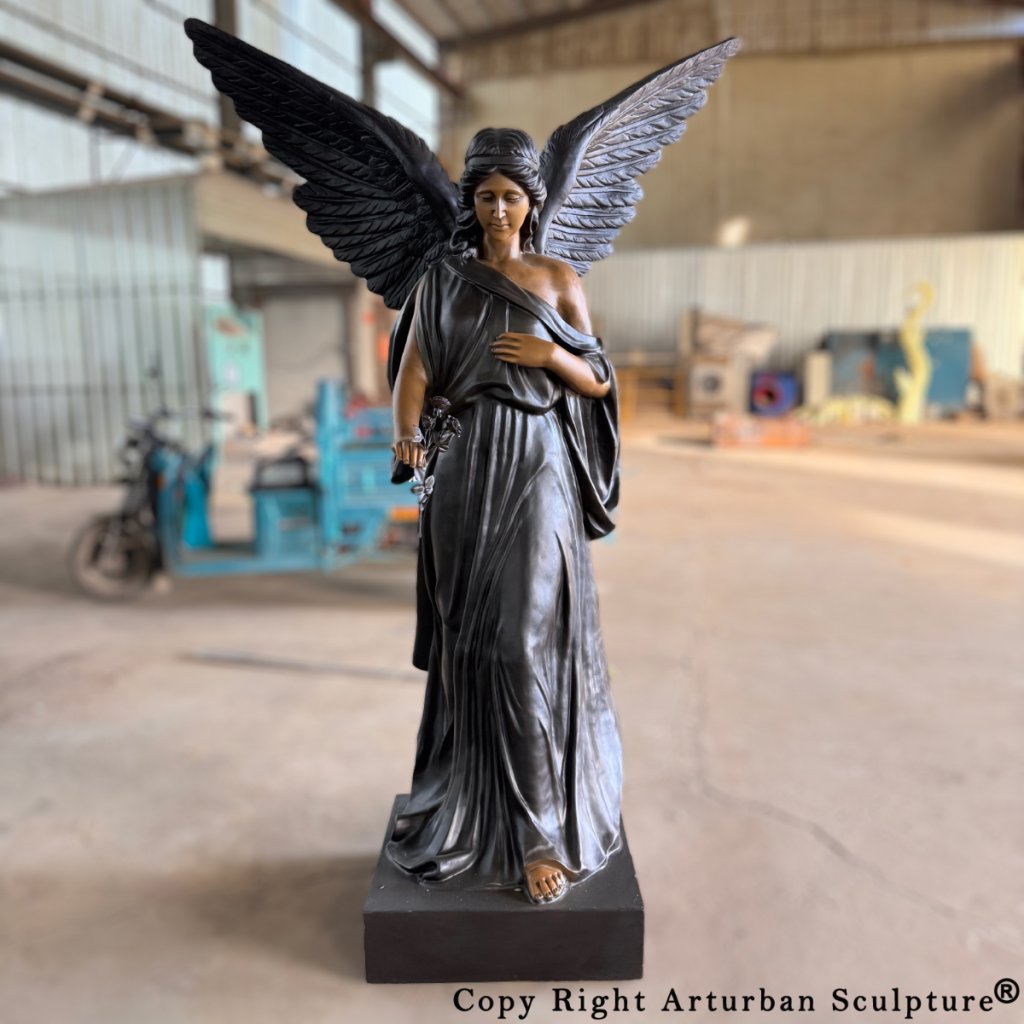
Content:
- 1. Why do so many people prefer life size bronze statues? Which bronze statues are commonly made in life size proportions?
- 2. Which type of bronze is best for life size bronze statues? Why is this type of bronze used for statues? What are its advantages?
- 3. What are the steps involved in making a life size bronze statues?
- 4. What are the common installation methods for life size bronze statues?
- 5. What are the maintenance and care methods for life size bronze statues?
- 6. How much does a custom life size bronze statue cost?
1. Why do so many people prefer life size bronze statues? Which bronze statues are commonly made in life size proportions?
Many life size bronze statues are created to commemorate important figures or events, while some depict animals. These life size statues accurately replicate the proportions of humans or animals, making the viewer feel more connected and realistic. This realistic visual effect can evoke strong resonance and emotional experiences.
Life size bronze statues often represent specific historical events, cultural symbols, or iconic figures, carrying deep historical and cultural significance. Because they are life size statues, viewers can gain a more direct understanding of history, culture, and social changes through these statues.
Which bronze statues are commonly made in life size proportions?
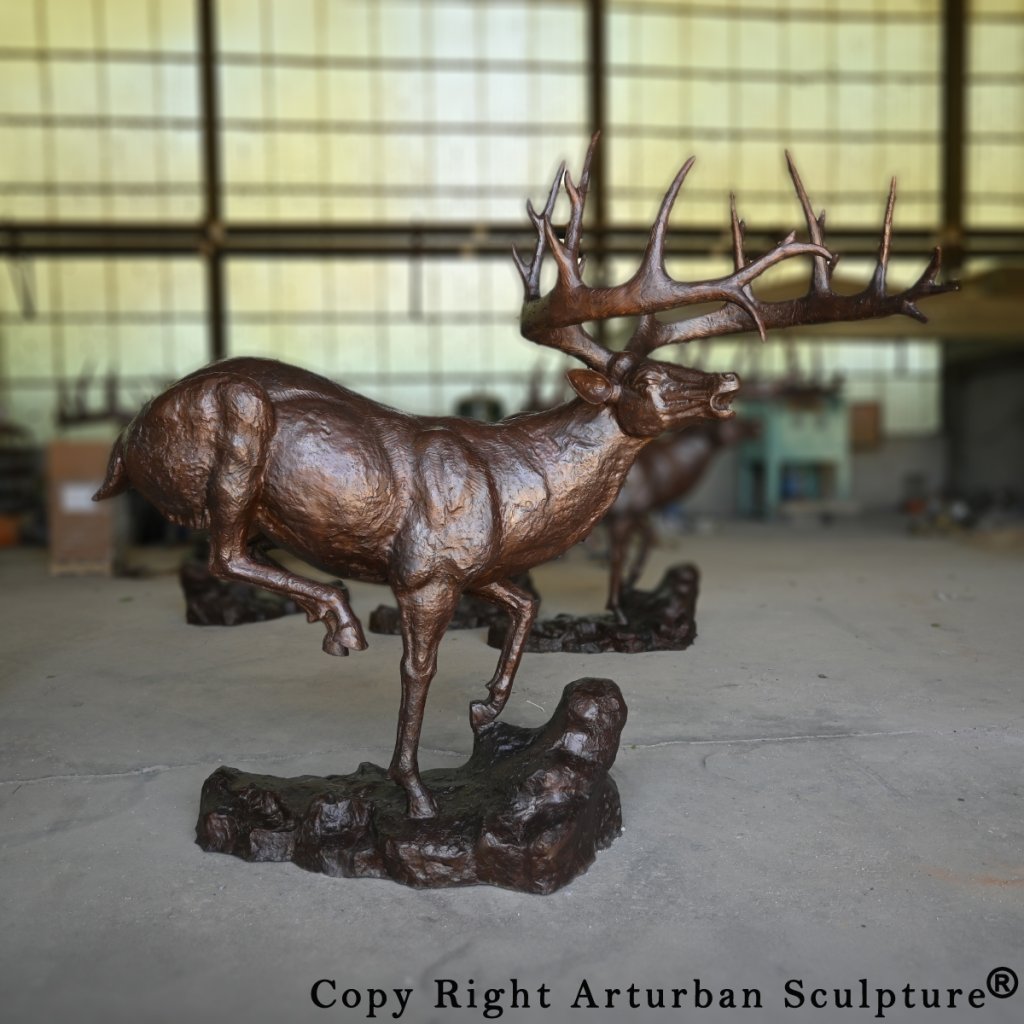
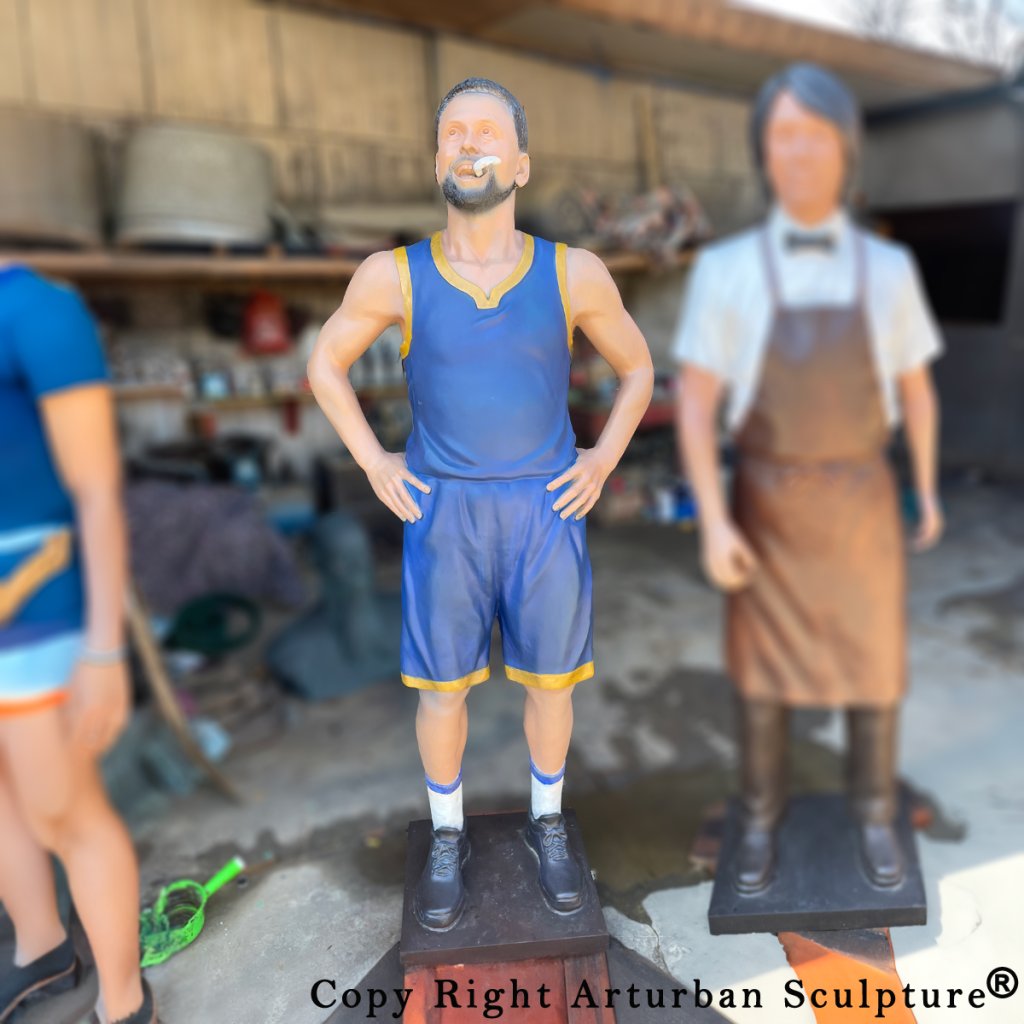
Common life size sculptures typically depict animals and people.
For instance, life size human statues provide viewers with a better sense of immersion. Life size animal statues make the artwork more lifelike, giving the impression of seeing a real animal.
2. Which type of bronze is best for life size bronze statues? Why is this type of bronze used for statues? What are its advantages?
Based on our many years of experience in bronze sculpture casting, we believe that using bronze with an 85% copper content is the most ideal. This 85 bronze contains 85% copper, 5% lead, 5% zinc, and 5% tin. Why do we use this specific bronze alloy ratio for casting sculptures?
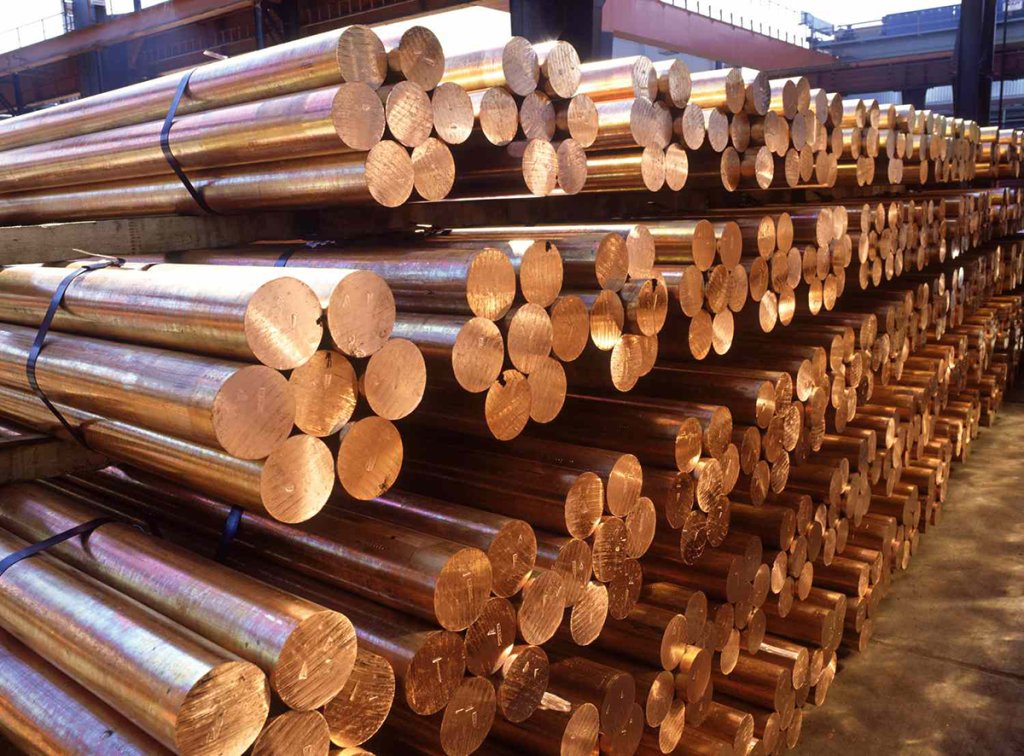
2.1 Why is 5% lead added when casting bronze statues?
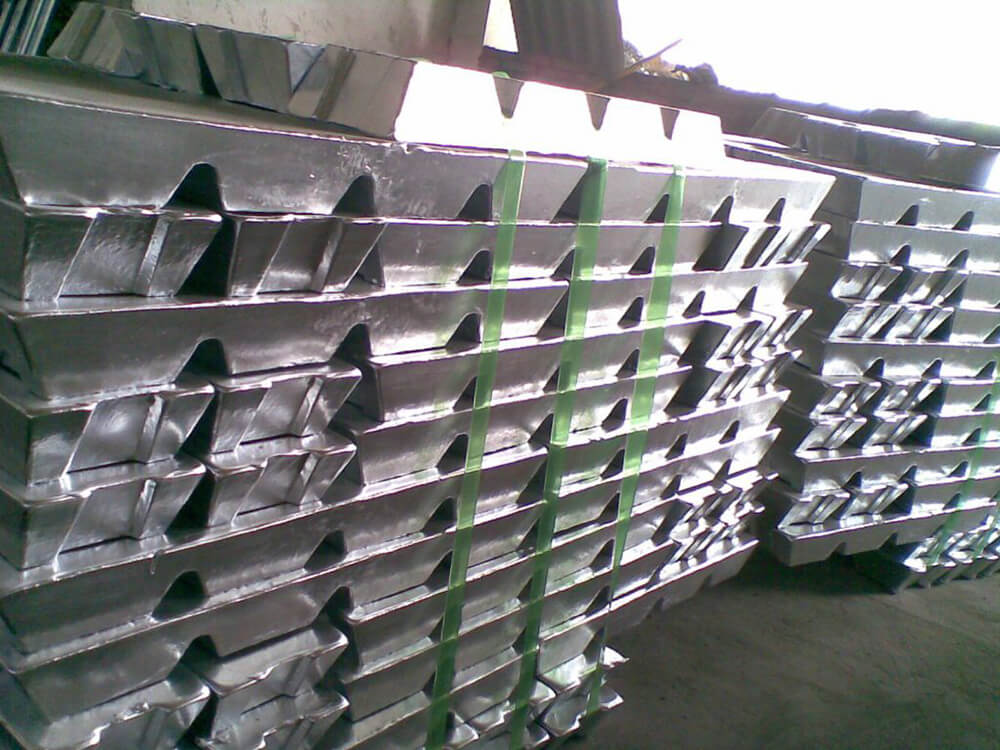
Improved fluidity: Lead enhances the fluidity of the alloy in its liquid state, making it easier to fill molds and form intricate details.
Enhanced machinability: Lead makes bronze easier to cut and process, facilitating subsequent carving and polishing.
2.2 Why is 5% zinc added when casting bronze statues?
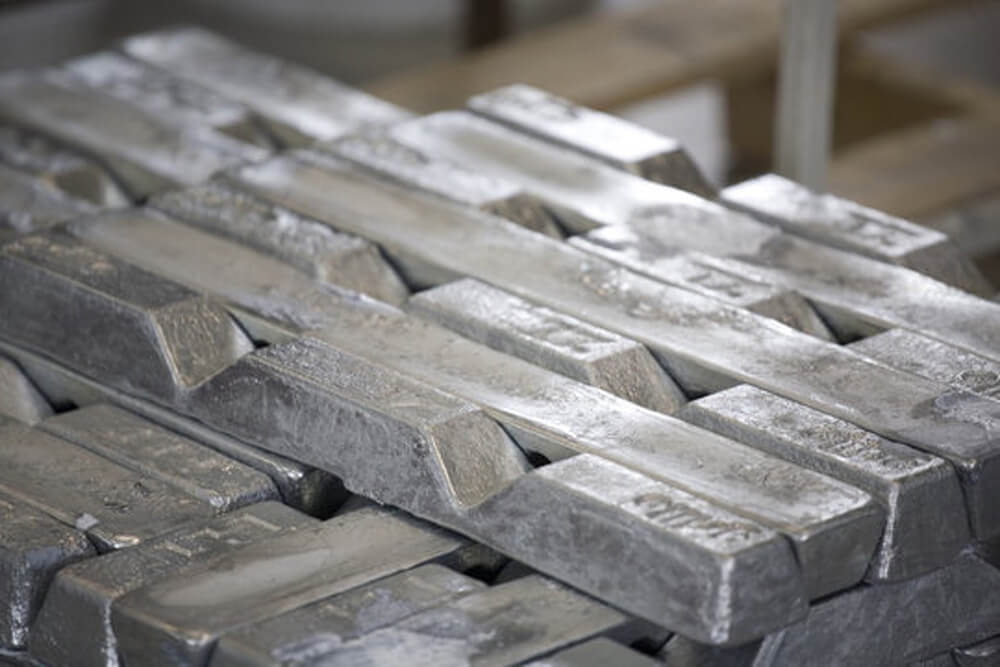
Increased corrosion resistance, hardness, and strength: The addition of zinc enhances the hardness and strength of bronze, making the statues more robust and durable. Zinc also improves the corrosion resistance of bronze, extending the lifespan of the statues.
Improved fluidity: Zinc also improves the fluidity of the alloy, aiding in detailed casting work.
2.3 Why is 5% tin added when casting bronze statues?
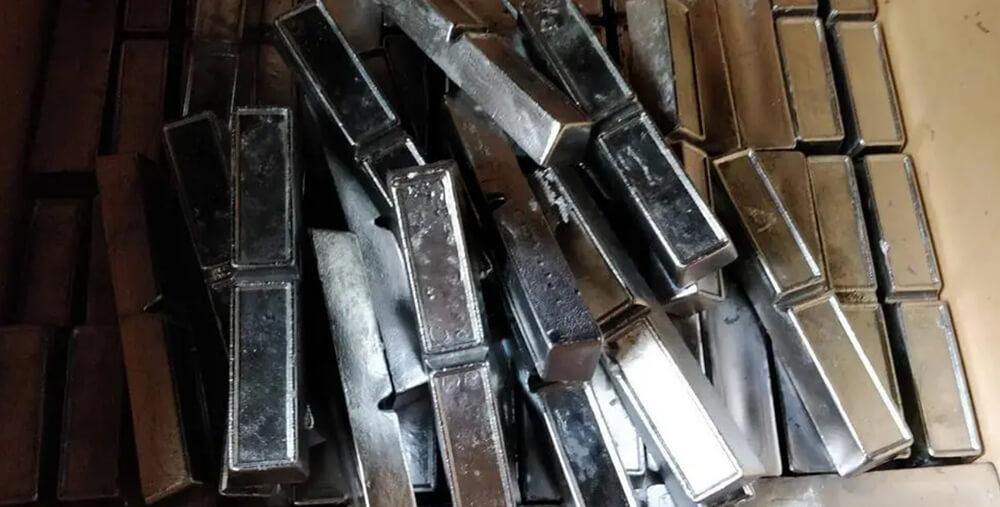
Improved fluidity and reduced melting point: Tin significantly enhances the fluidity of the alloy and further lowers its melting point, ensuring a smooth casting process and making it easier to fill complex molds.
Increased corrosion resistance: Tin helps prevent oxidation and corrosion, protecting the surface of the statues.
In Conclusion: By simultaneously adding lead, zinc, and tin, a comprehensive improvement can be achieved in terms of lowering the melting point, enhancing fluidity, increasing hardness and strength, and improving corrosion resistance. This ensures that the bronze alloy exhibits excellent overall performance during casting and use. Consequently, it guarantees detail and quality, as the addition of these metals ensures that the castings have fine surface details, reduces casting defects such as porosity and shrinkage, and improves the consistency and aesthetic appeal of the finished product.
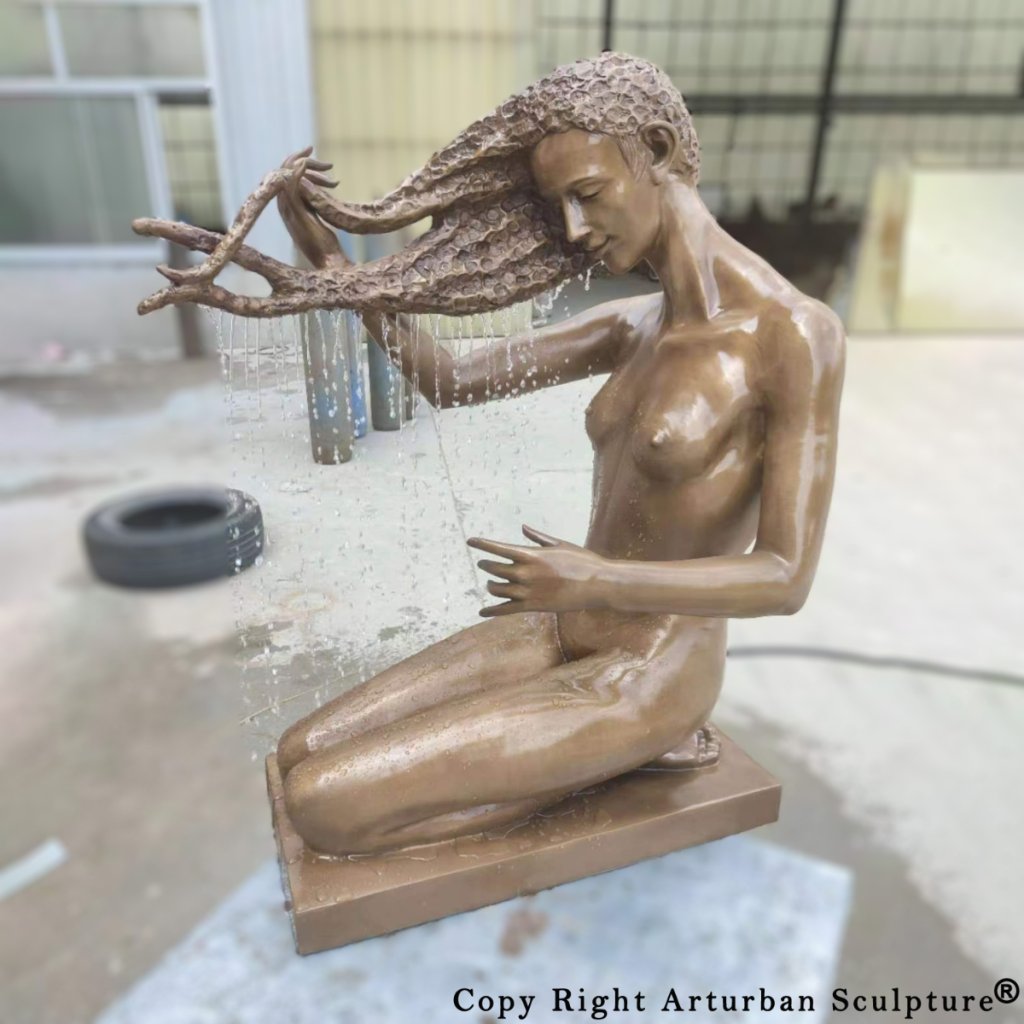
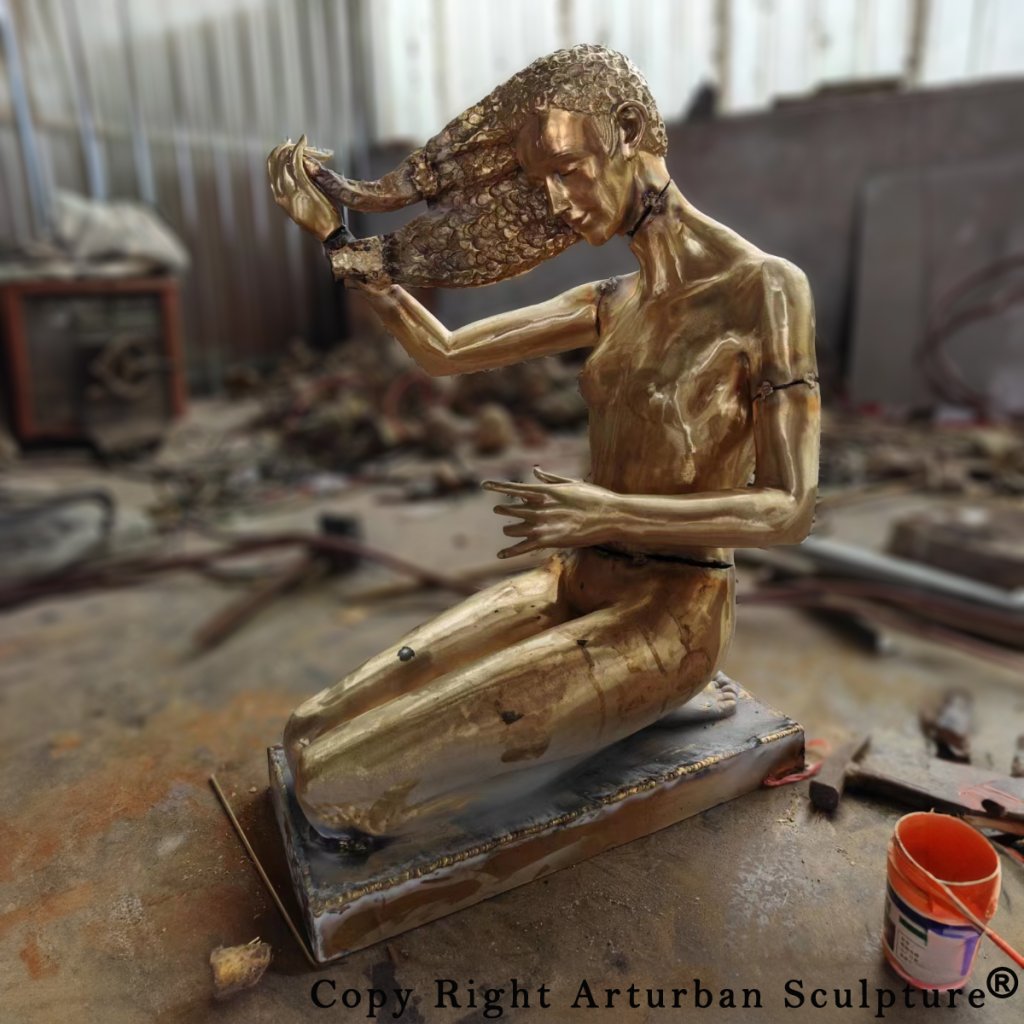
3. What are the steps involved in making a life size bronze statues?
3.1 Model Making: Model include Clay model and 3D Printing
Clay Mold: This involves creating a prototype of the statue using clay. Sculptors manually shape and carve the clay using tools, gradually refining the form and details. This process can take from several days to several weeks, depending on the complexity of the statue.
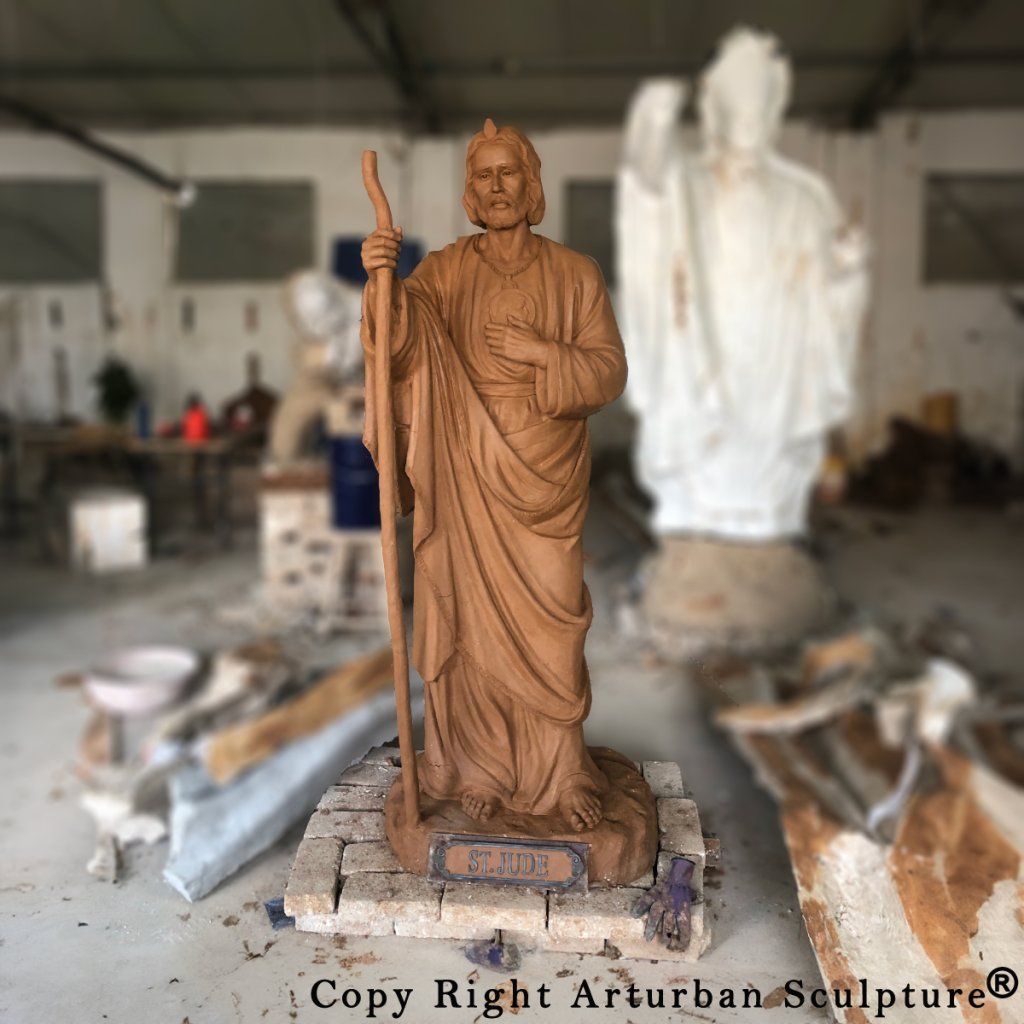
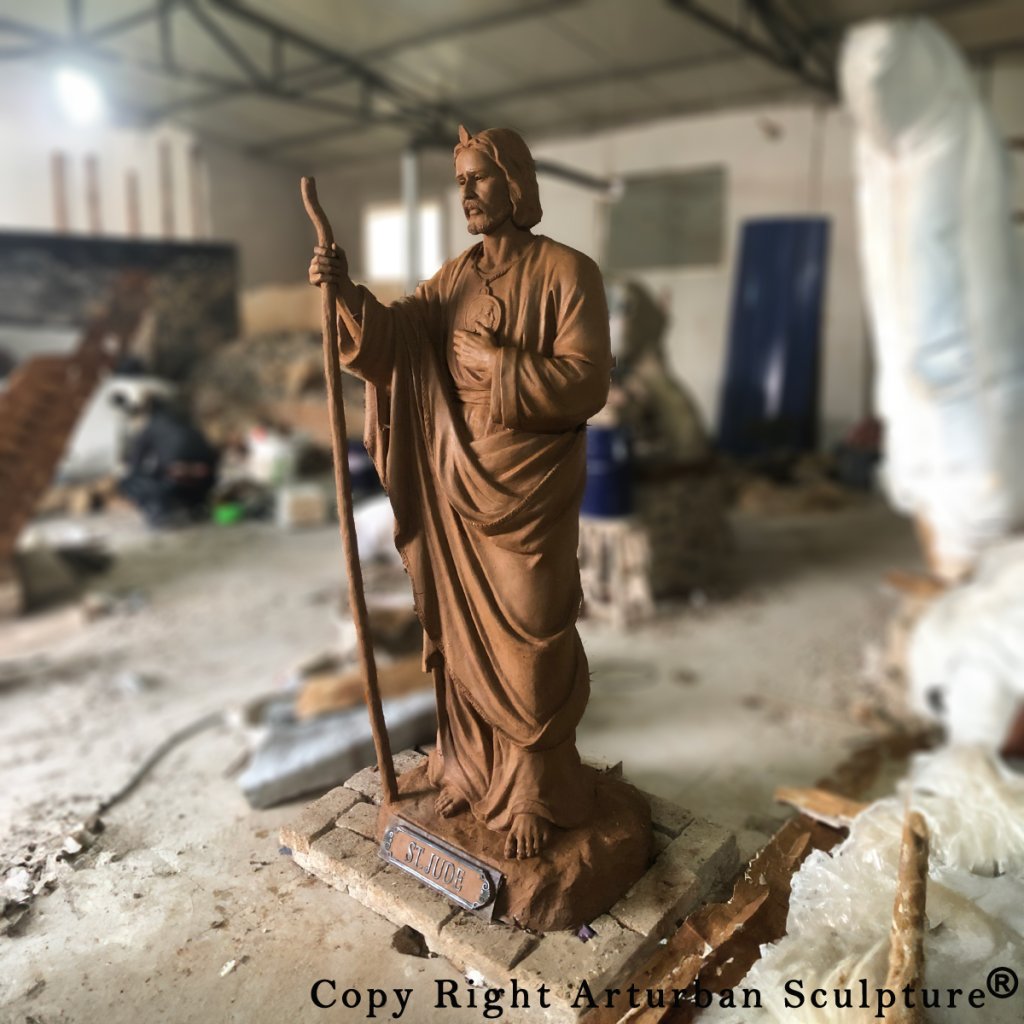
3D Printing: With technological advancements, 3D printing has also been applied to the creation of bronze statues. By designing a 3D model of the statue using 3D modeling software and then printing it with a 3D printer, models can be produced quickly and accurately.
3D Printing 3D Printing
3.2 Duplicate the mold:Using Silicone or Plaster for Mold Making
Silicone Molds: Liquid silicone is applied over the surface of the model, silicone seeps into all fine textures to form an accurate negative mold. Once the overmolding, a layer of plaster or fiberglass is typically added externally to increase strength.
Silicone Molds Silicone Molds
Plaster Molds: Plaster molds are more cost-effective and suitable for creating simpler or larger statues, as they provide more structural support.
Plaster Molds Plaster Molds
3.3 Create a wax model
Wax Injection: Hot molten wax is injected into the silicone or plaster mold, ensuring that every detail is filled with wax. After the wax cools and hardens, the wax model is removed, precisely replicating the details of the original model.
wax mold wax mold wax mold
Refining the Wax Model: Once the wax model is removed, sculptors meticulously refine it, removing any bubbles, gaps, or imperfections. (As shown in the video below)
3.4 Create a shell or make a sand mold
Shell Making (As shown in the video below): For small or complex pieces, precision casting is commonly used. The wax model is repeatedly coated with a quartz slurry to ensure the sculpture’s details. The first layer of quartz must be the finest slurry, the second layer is a protective layer, and the third layer is a high-temperature resistant layer, made from a high-temperature resistant slurry. For small pieces, about 5-6 protective layers are sufficient to prevent deformation during bronze casting. For slightly larger or medium pieces, 6-7 protective layers are needed. For large pieces, 9-13 layers are required. Each layer of slurry is allowed to dry before applying the next, enveloping the wax model layer by layer in quartz slurry until a sturdy shell is formed. This process usually involves multiple heating and cooling cycles to ensure the ceramic shell’s strength and durability. With over twenty years of casting experience, Arturban Statue has continually refined and perfected this shell-making method over the years.
Sand Molding (As shown in the video below): The wax model is placed in a sandbox and covered and compacted with fine sand. To ensure the statue’s details, a high-temperature resistant coating is applied to the surface. This step is crucial as it determines the fineness of the statue’s texture and details. This sand molding method is mainly used for larger castings, where the sand provides support and insulation.
3.5 Burn out the shell to remove wax and cast molten bronze
Burnout – Wax Removal (As shown in the video below): The ceramic shell is heated by placing it in a high-temperature kiln. The temperature of the kiln is gradually increased to prevent the ceramic shell from cracking due to sudden temperature changes. The temperature usually rises from room temperature to between 700°C and 900°C. When the temperature reaches the melting point of the wax (typically between 100°C and 200°C), the wax inside starts to melt and flow out of the ceramic shell. This process is called “wax removal.” The wax flows out through pre-made wax removal holes, leaving a cavity in the shape of the future bronze casting. The ceramic shell is further heated to a higher temperature (typically between 700°C and 900°C) to enhance its strength and heat resistance, enabling it to withstand the high temperatures and metal flow impacts during the subsequent casting process.
Bronze Casting: The high-temperature molten bronze liquid is poured into the prepared shell or sandbox. The temperature of the molten bronze liquid needs to be controlled within an appropriate range to ensure it flows sufficiently and fills the entire cavity. During the casting process, it is crucial to control the pouring speed and position to avoid the formation of bubbles and defects.
3.6 Break the shell
This refers to the process of removing the casting shell. These shells, formed by coating with quartz sand and refractory materials as described earlier, provide a mold for the molten bronze during casting. After casting and cooling, tools such as pneumatic hammers, hydraulic hammers, or vibrating tables are typically used to break and remove the shell, revealing the true form of the bronze statue. The shell removal process must be done carefully to avoid damaging the surface of the casting. For some complex-shaped castings, manual tools may be needed to complete the shell removal. Make sculpture clean and smooth
3.7 Sandblasting
A sandblaster uses compressed air to blast abrasive particles onto the metal surface, cleaning and polishing the bronze statue to make the surface clean and smooth. Water sandblasting can also be used, employing a specialized high-pressure water jet to clean and smooth the statue’s surface.
3.8 Welding and polishing
Welding: If the statue is cast in multiple parts, these parts need to be welded together. The weld points must be finely ground to ensure that the seams are smooth and inconspicuous.
Polishing: Depending on the requirements, the statue’s surface is sanded and polished using sandpaper of varying grits, grinding tools, and polishing agents. This process makes the surface smooth and shiny, removing any imperfections and enhancing the statue’s aesthetic appeal.
3.9 Make Color
Chemical Coloring (As shown in the video below): Chemical agents (such as copper sulfate, silver nitrate, etc.) are used to color the surface of the statue, producing different colors and effects.
Painting and Spray Painting (As shown in the winged horse images below): After painting or spray painting, a clear protective varnish is applied to the statue’s surface to protect it from environmental effects, preserving its color and shine. Regardless of the coloring method, the final step involves waxing or applying automotive lacquer to protect the statue’s color. For chemical coloring, heat coloring can be used. A torch is used to heat the bronze statue, then special statue wax is applied. This method ensures that the statue is less prone to corrosion over time.
Using automotive protective clear lacquer makes the statue shinier and more reflective, The statue can also be placed for a long time without being corroded by humid air.
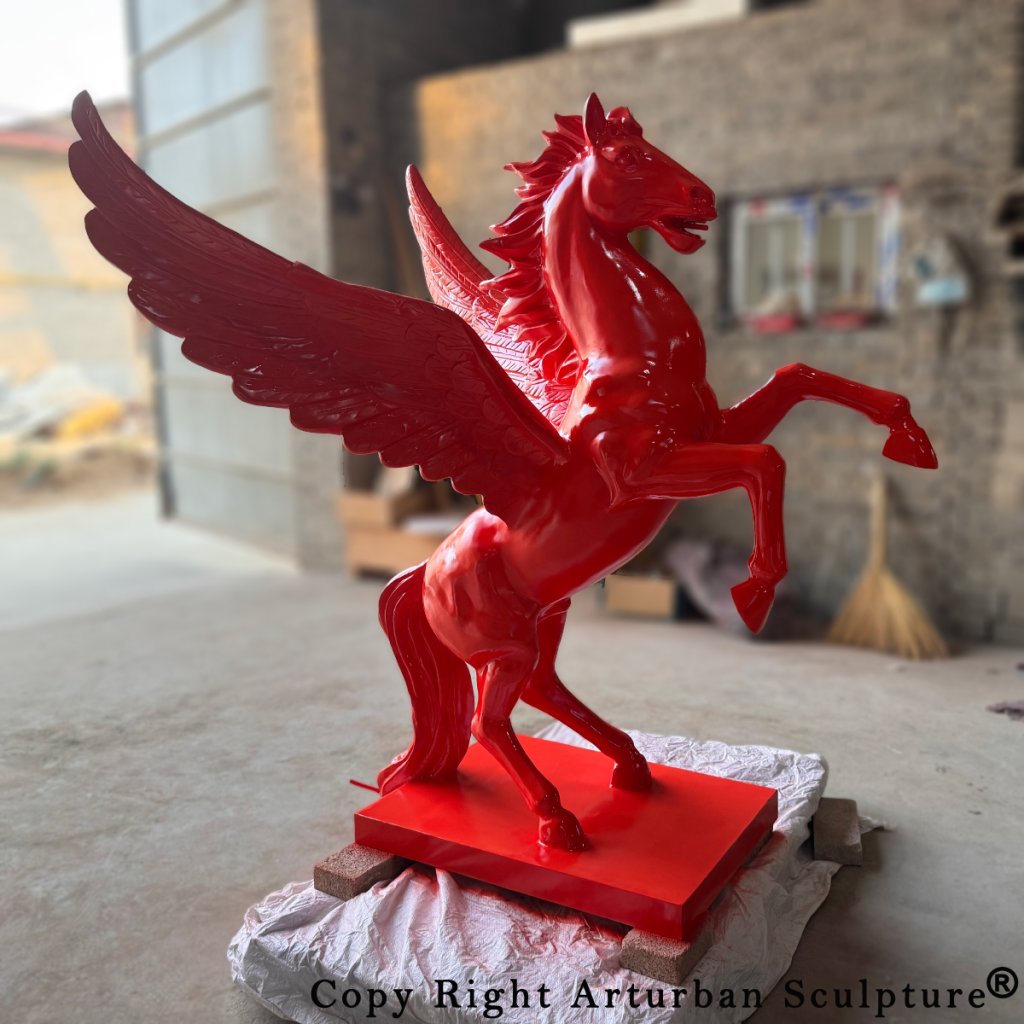
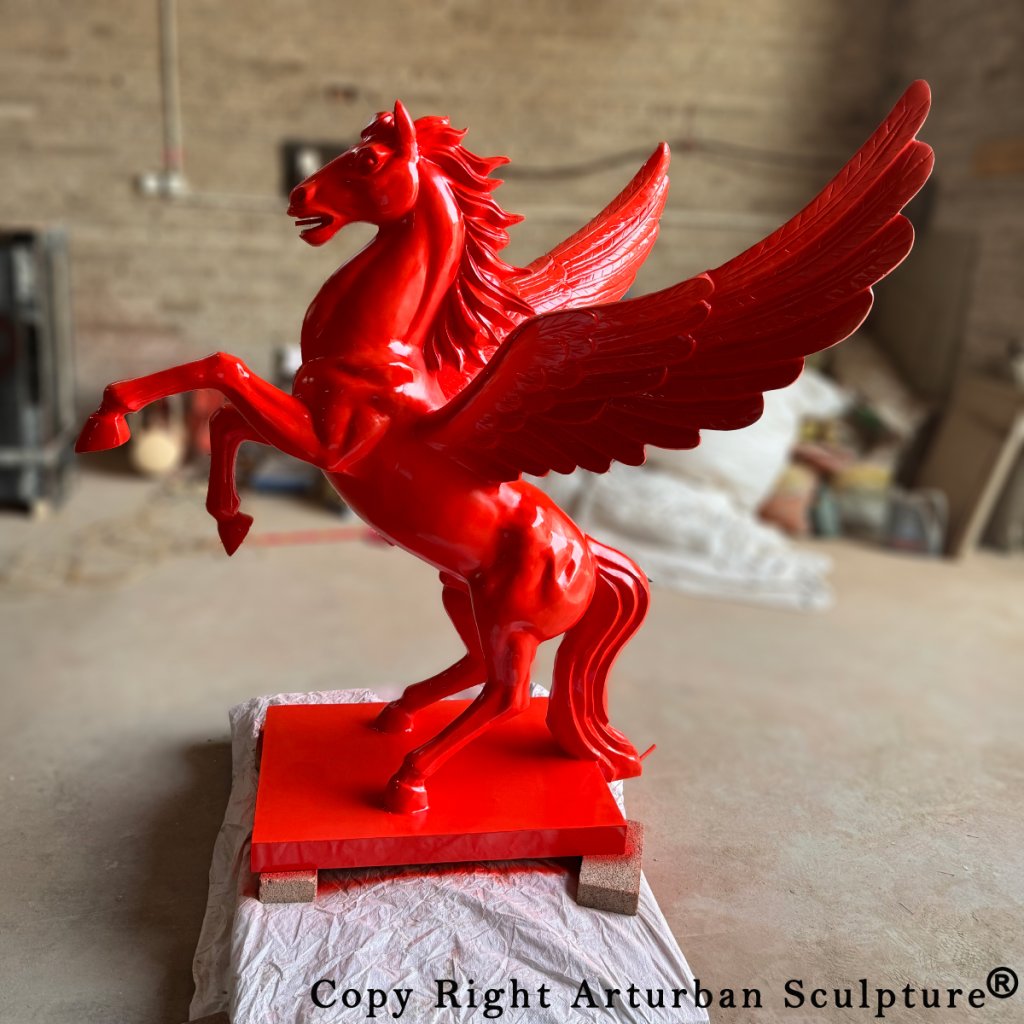
Arturban Statue offers various coloring methods according to customer needs. Based on actual customer requirements, the artists at Arturban Statue will provide the best coloring solution.
4. What are the common installation methods for life size bronze statues?
Embedded Installation: We design an embedded base at the bottom of the statue, usually 15-25 cm long (customizable based on customer requirements). This base is made of channel steel or rebar and can be embedded directly in concrete to securely fix the statue, preventing it from wobbling. (Just like the base of the sculpture in the following picture)
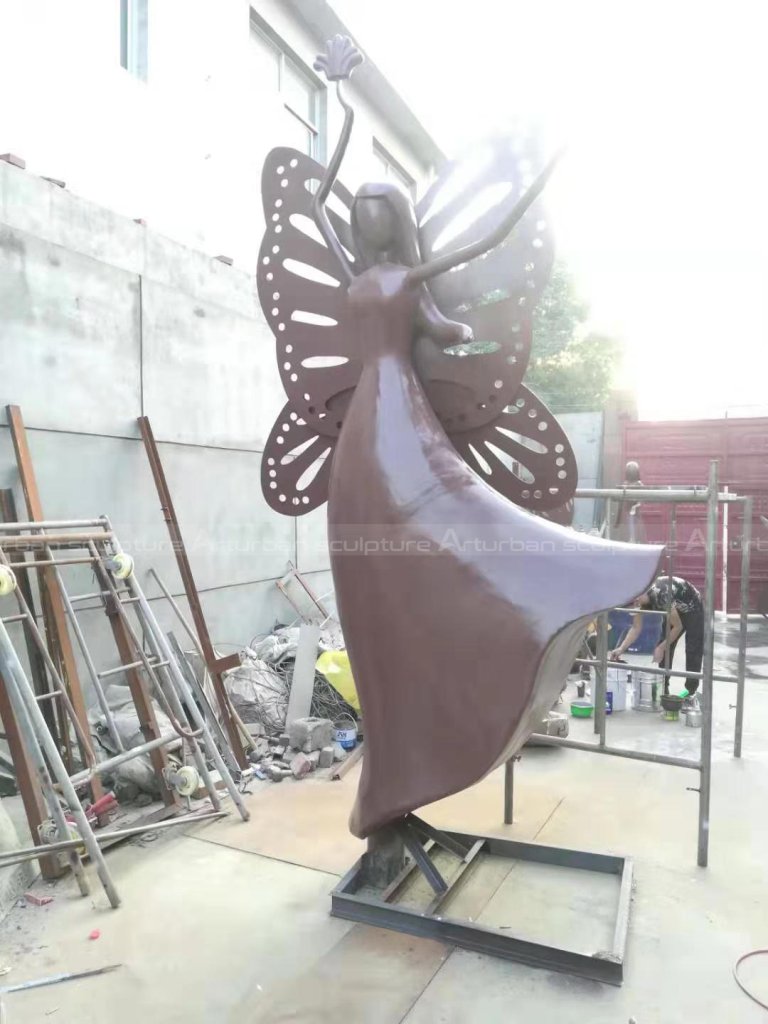
Screw Installation: Arturban Statue has found this to be a cost-effective and stable method. Most customers prefer this option. Nuts (4-10, depending on the statue’s weight, structure, and size) are welded to the bottom of the statue’s base. Screws with a diameter of 2.5-3.5 cm are then prepared. Upon receiving the statue, customers can directly screw it into the nuts and embed it in concrete. (As shown in the video below)
Free Stand: If the statue is to be placed indoors or outdoors without embedding, a flat base is made to allow the statue to stand securely on the ground or lawn. However, this method increases transportation and material costs. (Just like the base of the sculpture in the following picture)
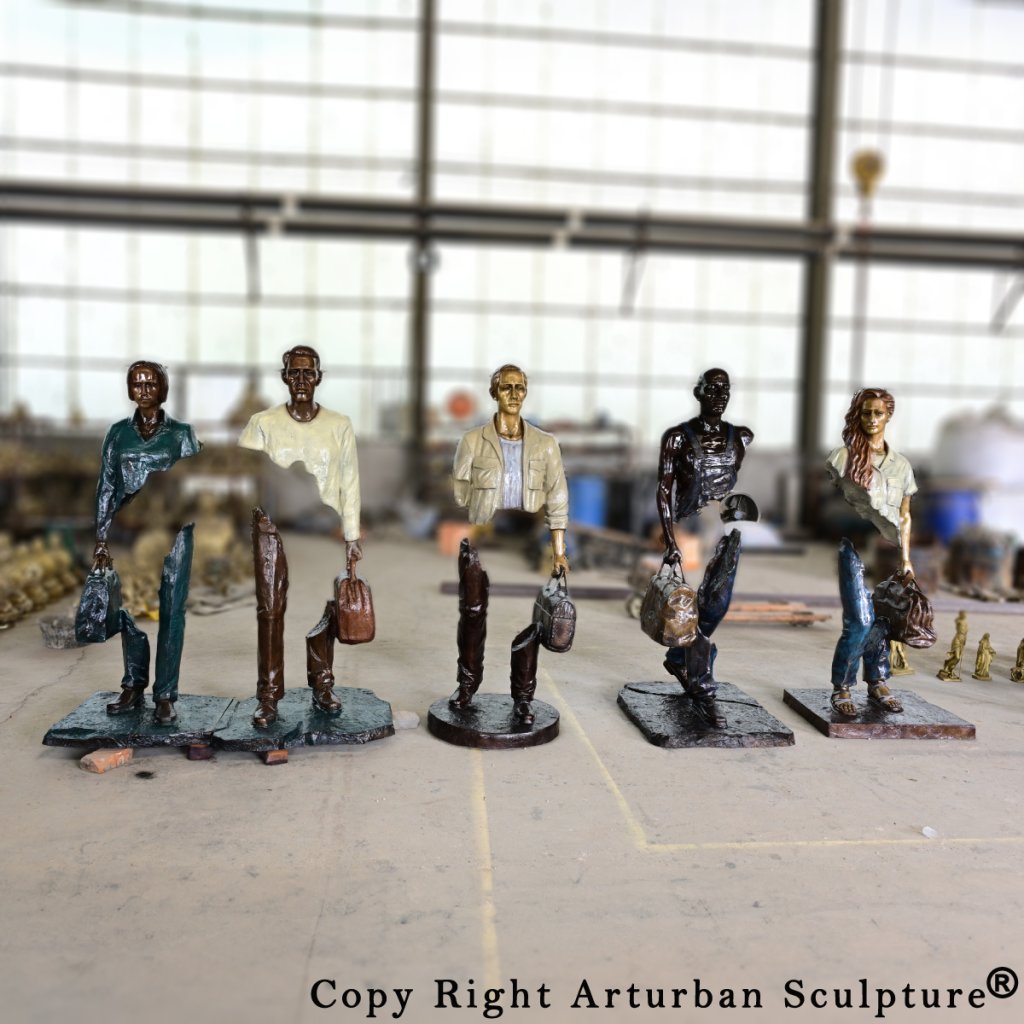
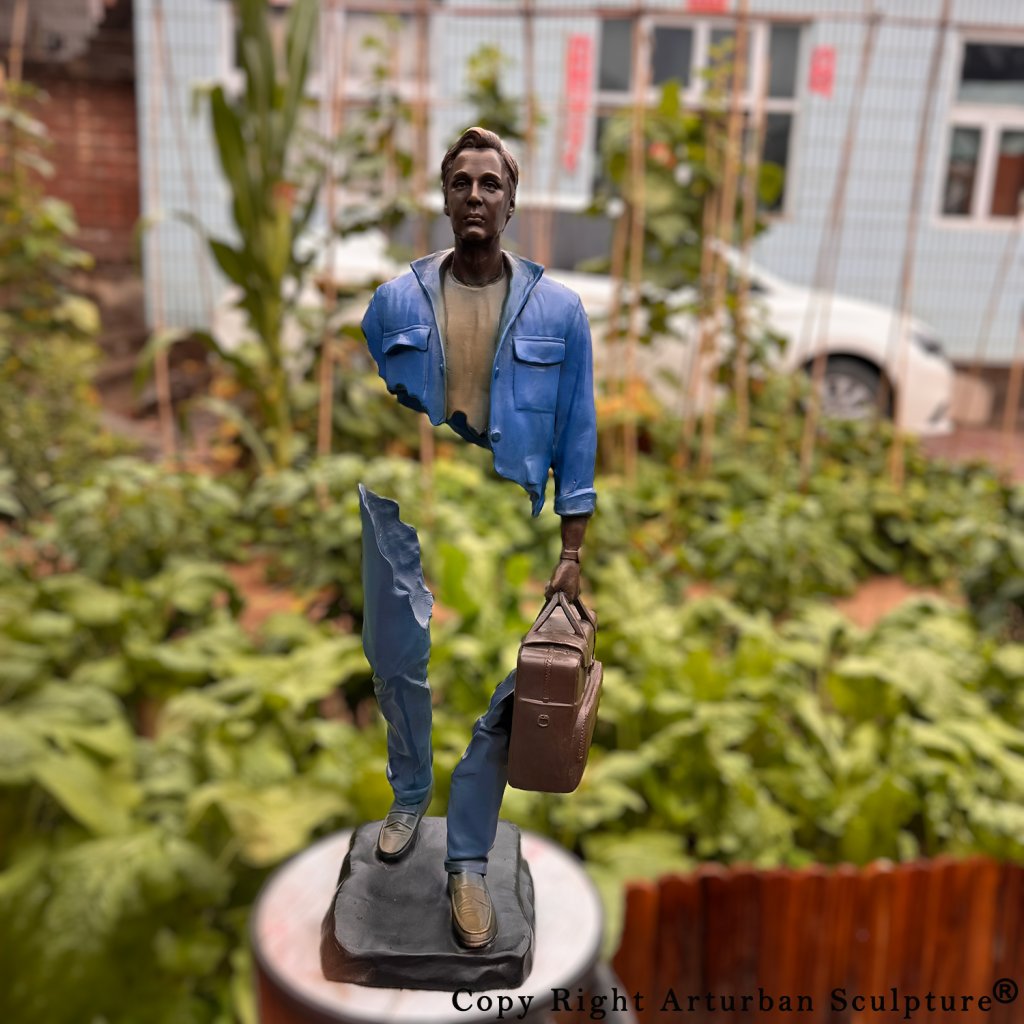
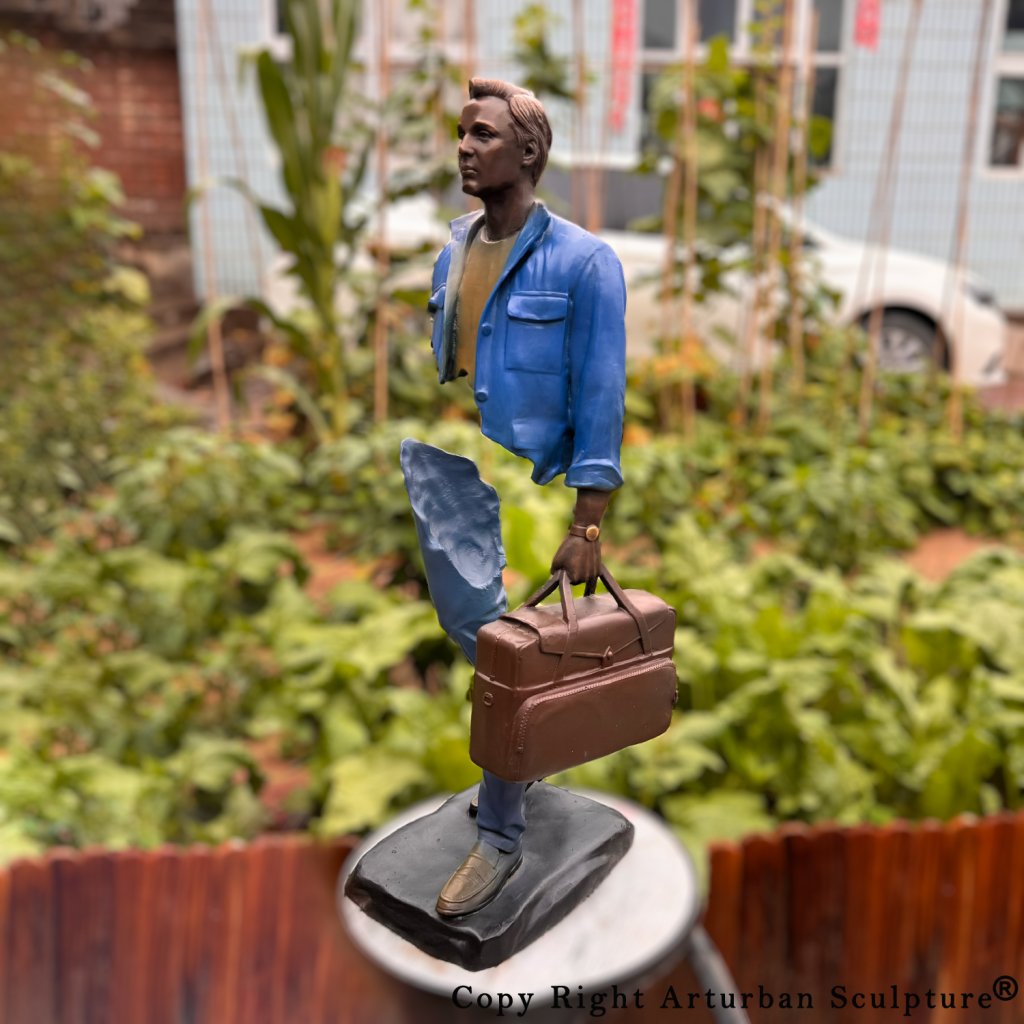
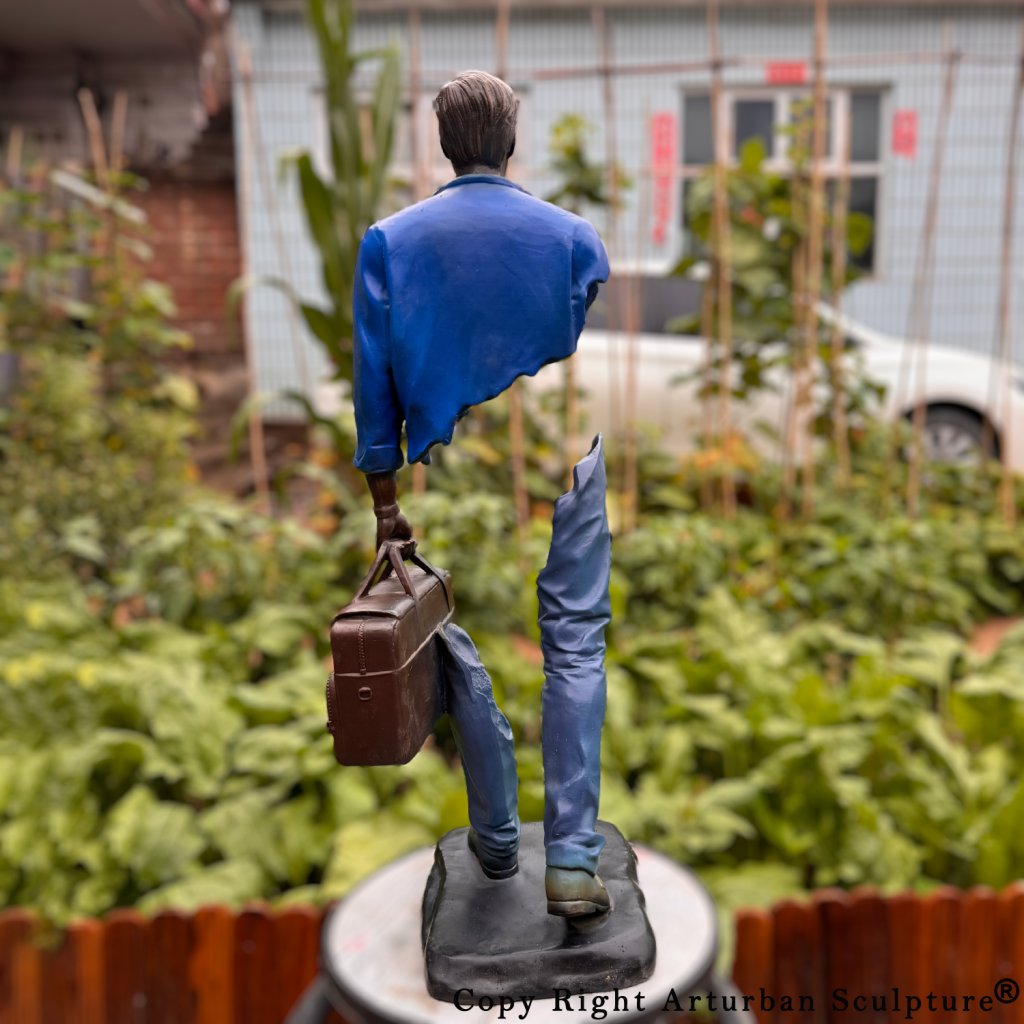
For life size bronze statues, but oversized statues, such as large elephants, giraffes, or prehistoric beasts, Arturban Statue also offers on-site installation services. The statue is divided into several parts, transported to the installation site, and then welded together, including the internal framework. After assembly, on-site coloring is completed.
5. What are the maintenance and care methods for life size bronze statues?
Generally, maintenance of life size bronze statues involves corrosion and rust prevention. This depends on the coloring process previously described. For chemically colored statues using the heat coloring and waxing process, regular rewaxing is needed to restore the factory finish. If the statue is damaged (e.g., intentionally broken or smashed), welding and grinding are required, followed by coloring, repeating the steps mentioned earlier. For older statues with complex damage, an analysis and tailored restoration plan are necessary. Arturban Statue offers free professional consultation for restoration solutions.
For bronze statues with painting + spray paint + automotive protective clear lacquer, if the color is damaged, the same color automotive paint is used for touch-ups, followed by spraying with automotive protective clear lacquer.
6. How much does a custom life size bronze statue cost?
Life size bronze Human Statues: Typically, the price ranges from $1600 to $20,000. For example:
life size bronze child statue life size bronze child statue
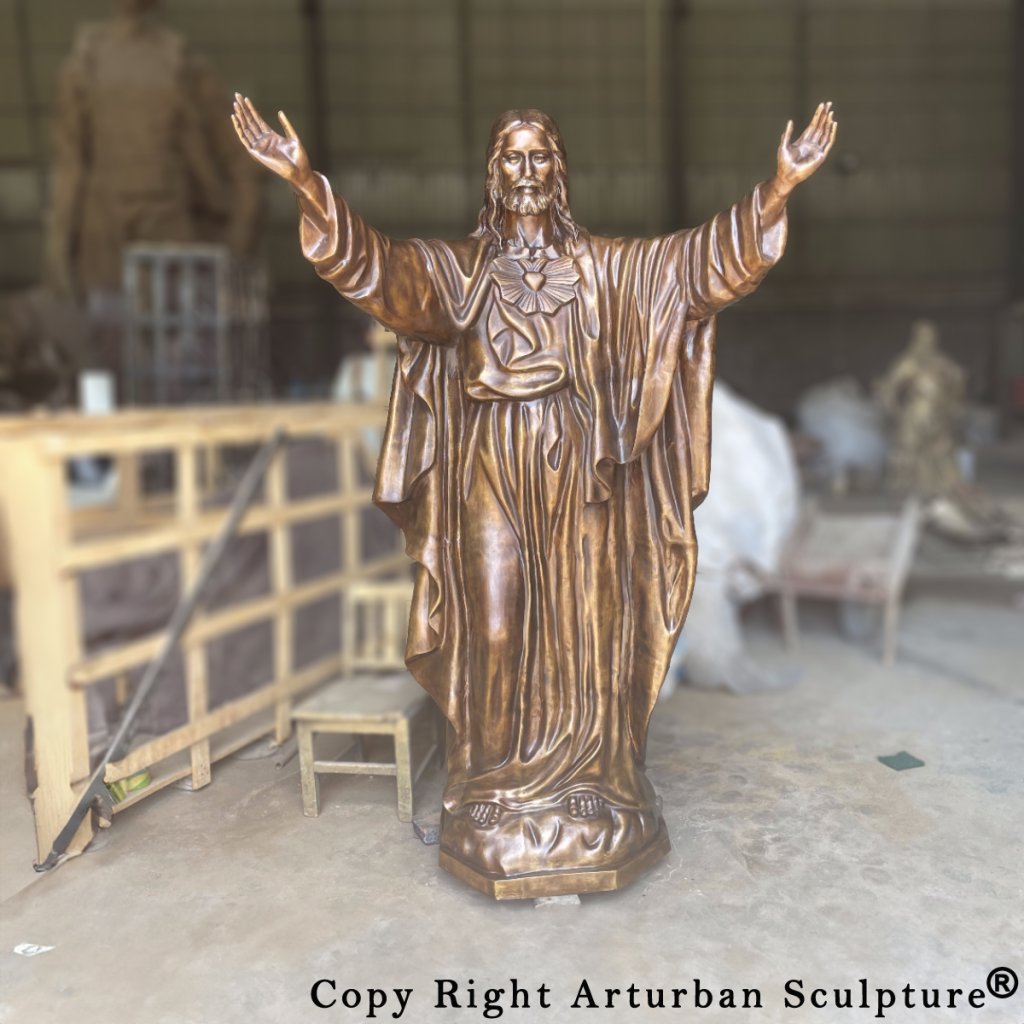
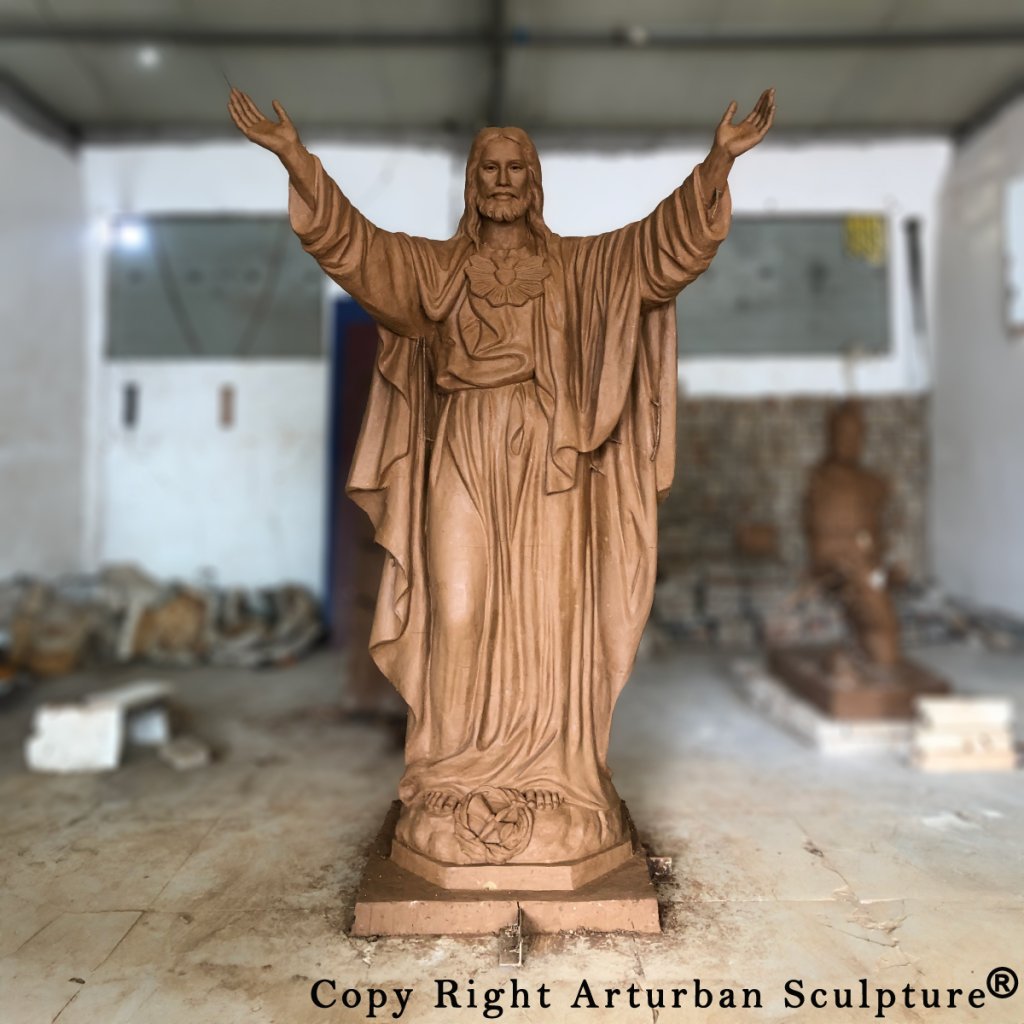
- A life size bronze child statue around 1.2 meters tall costs approximately $1600.
- A life size bronze adult statue around 1.8 meters tall costs approximately $2200.
- The cost mainly depends on the design. If the statue includes additional elements such as a chair or other handheld items, the price may increase accordingly.
Life size bronze animal Statues: Typically, the price ranges from $600 to $20,000. For example:
life size bronze statue of a small Pug dog
life size bronze statue of a large gorilla
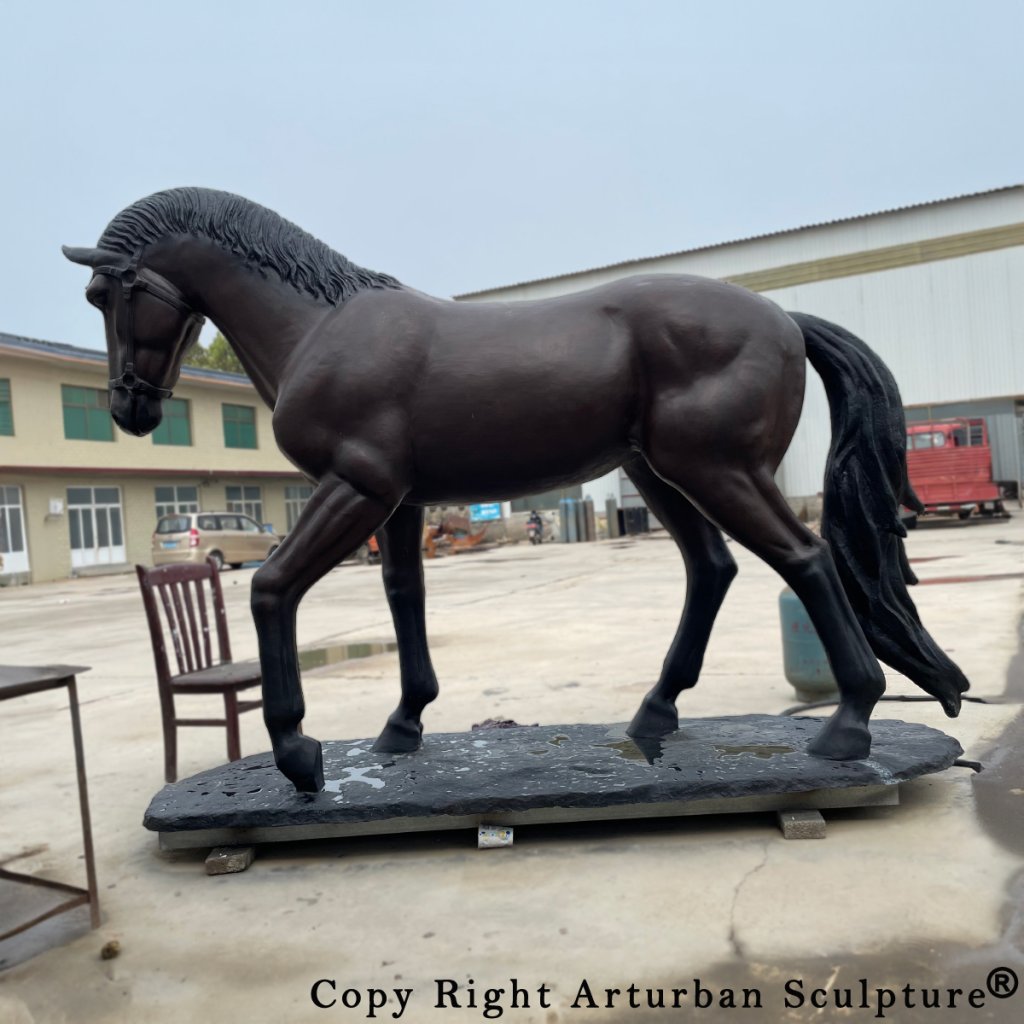
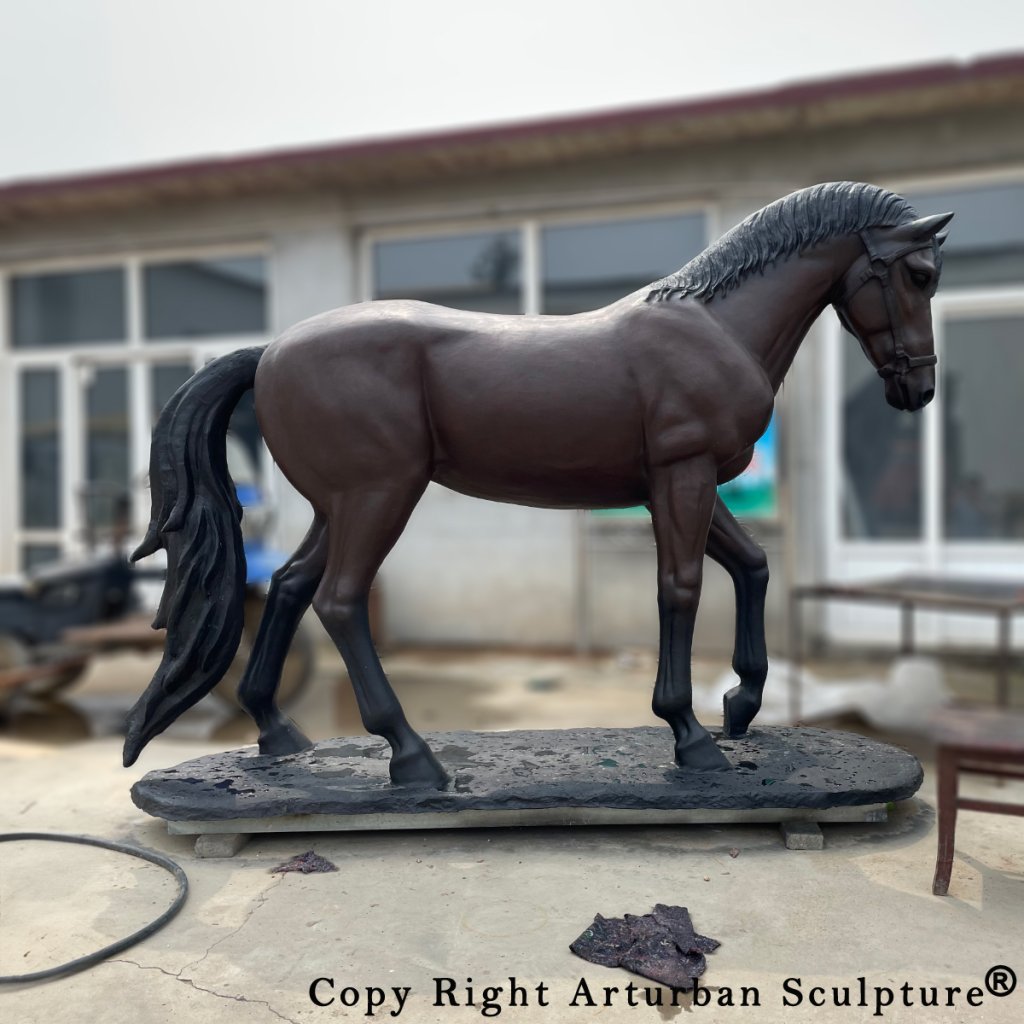
- A life size bronze statue of a small Pug dog, with a length of 60 cm, costs approximately $600.
- A life size bronze statue of a large gorilla, with a height of 1.7 meters, costs approximately $4000.
If you have photos, design drawings, or ideas for the bronze statue you want, you can contact us, and we will provide a free quote.
Send us your requirements now, we will reply to your email within 24 hours